The world’s leading steel producers are using HERZOG systems for quality control of their products. Our solutions guarantee the optimal preparation of iron, steel and slag samples for all relevant analyzing methods including optical emission spectroscopy (OES), X-ray fluoroscopy (XRF) and combustion analysis.
HERZOG Steel solutions are exactly adjusted to the needs of our customers. Sample transportation, handling and preparation are optimized to achieve the maximum level of quality and the shortest processing time. Equipment, software and interfaces are fully customizable to the individual requirements of each client. HERZOG is the perfect partner for implementing integrated solutions tailored to the individual sample types, local infrastructure, analyzing methods and devices, as well as level 2 system.
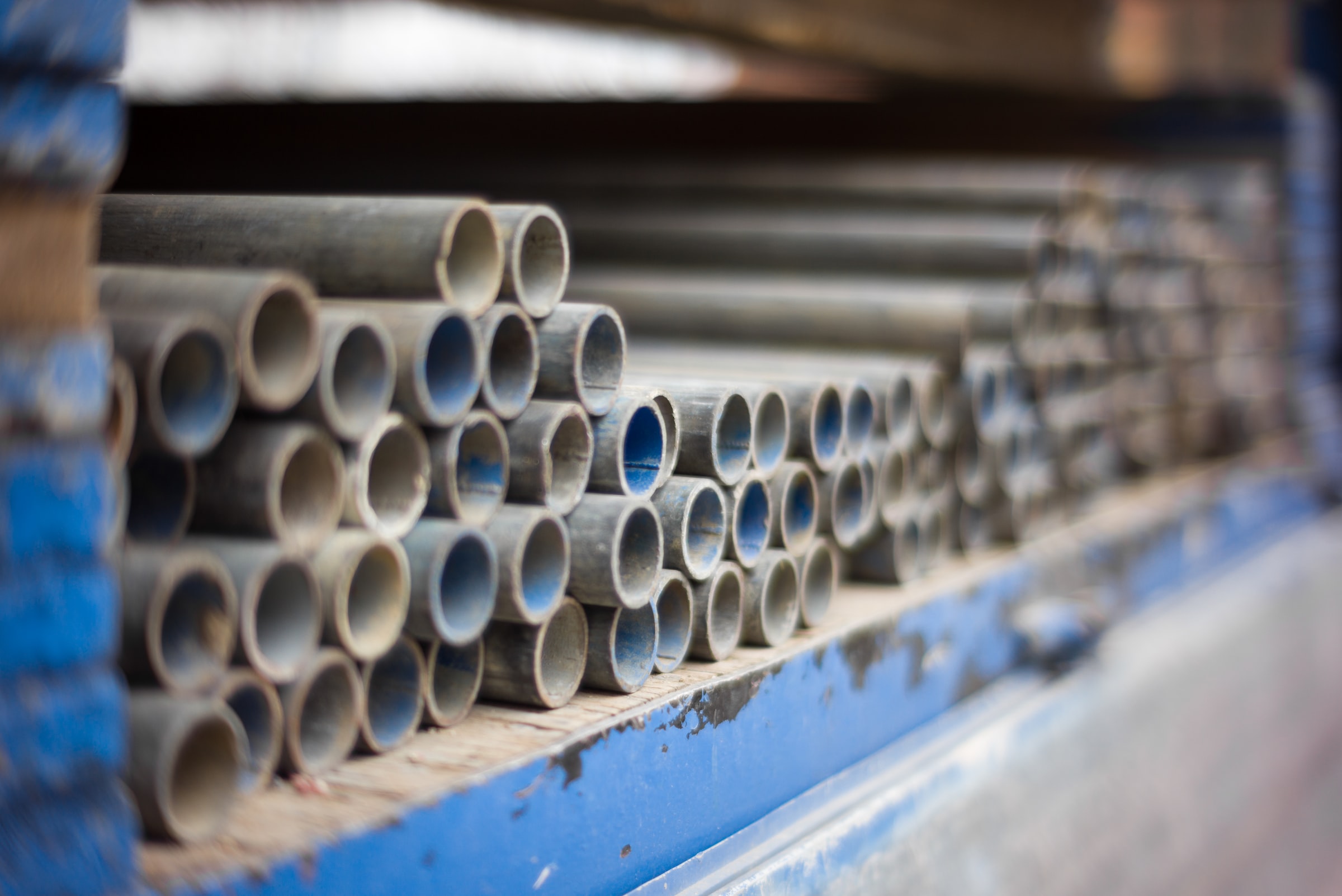
SAMPLE PREPARATION
For metal analysis in particular, the sample surface must be perfectly prepared because any spectroscopic analysis can only be as good as the quality of the samples. HERZOG offers a wide range of products that ensure an excellent prepared sample surface and therefore a high quality analysis.
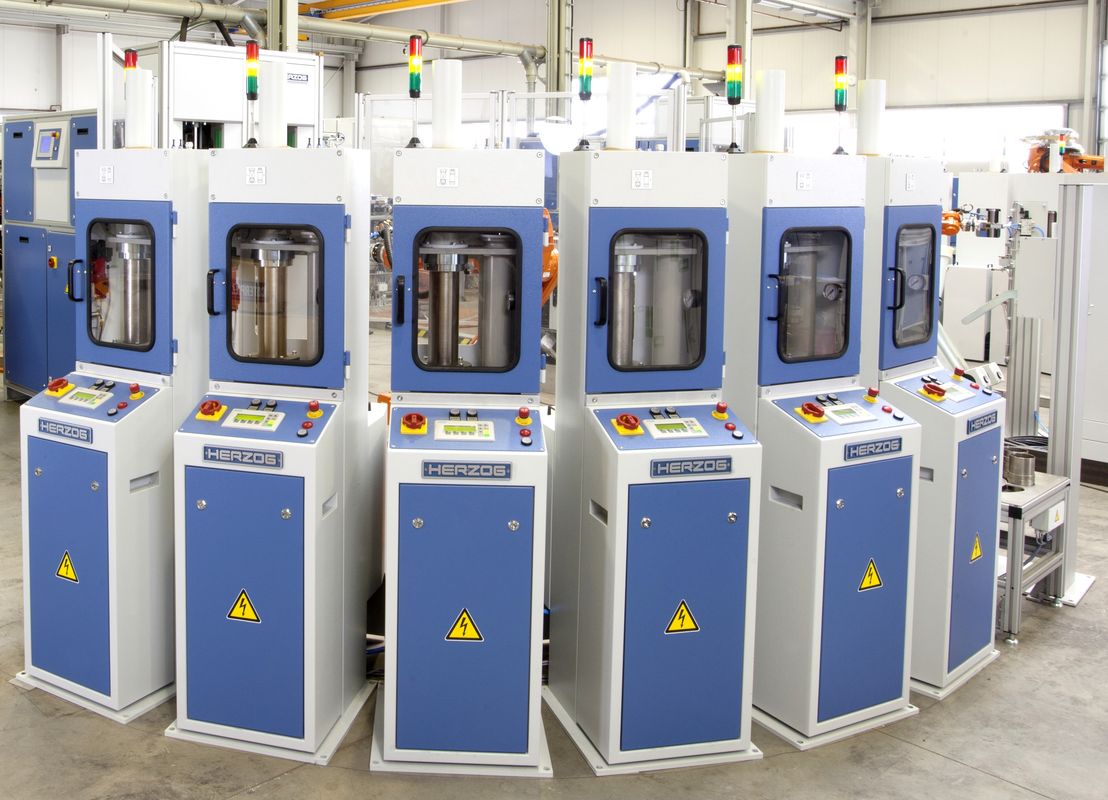
PNEUMATIC TRANSPORT
The pneumatic tube installation enables the transport of carriers containing metallic and slag samples from the production site to the central laboratory. The technology is based on quick transportation using air as power source. Usually, the pneumatic system can make use of compressed air that is abundant in steel plants.
The speed of the pneumatic carrier is up to 20 m/s. In case of specially configured pneumatic systems and air tubes, an even higher velocity is possible. The standard external diameter of pneumatic tubes is 80 mm whereas the internal diameter is 75 mm. At special request, systems with larger diameters are available as well.
To allow the fastest possible transport, there is a normally a direct connection between the pneumatic stations in the steel work and the laboratory. Alternatively, diverters can be integrated to allow transportation of carriers from a sending station to different receiving stations.
According to the sample type, different pneumatic carriers are available. For cold powder material and other light samples, we use carriers made from plastic. For hot powder and steel or iron samples, carriers are made from aluminium. For transportation of metallic samples, tailor-made inserts are used. This allows the reliable sample handling in fully automatic systems while increasing lifetime of carriers.
On the plant site, the steel worker selects the sample ID from the terminal screen of the pneumatic station, loads the carriers with iron and steel samples, slag, pins or other material, and starts transport. In the laboratory, carriers are unloaded in the pneumatic station or special unloading/ transfer stations containing additional modules like, e.g., cooling unit for hot metallic samples. After emptying, the carrier is locked and sent back to the plant station.
The control of the pneumatic system is due to the coordinated interaction between the PLC of the pneumatic station, the Scada system (PrepMaster) and the level 2 system of the client. The intelligent control of the system enables the efficient and quick sample transport into the laboratory.
PNEUMATIC TUBE INSTALLATION WITH COMPRESSED AIR AND DIVERTER
1. Sending station HR-HSK/B (plant)
2. Receiving station HR-LSM (laboratory)
3. 2-way diverter
4. Set of tube connections for compressed air/laboratory station
5. Set of tube connections for plant station
6. Profinet cable / Optional: Optical link
7. PrepMaster terminal (optional)
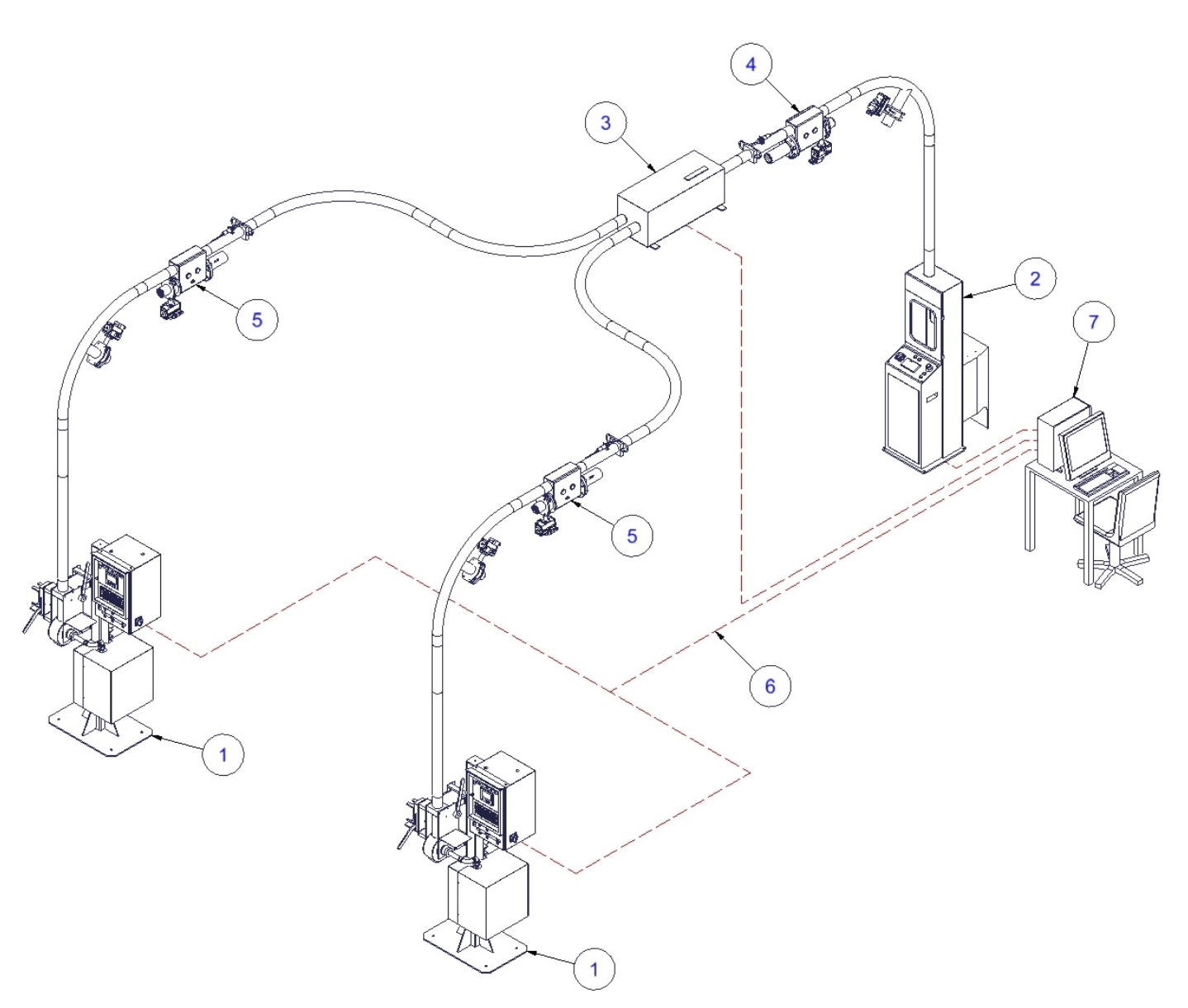