HERZOG is one of the cement industries’ leading partners in the development and establishment of laboratory systems. Innovative production processes as well as the increasing diversification of cement types involve higher demands on laboratory systems.
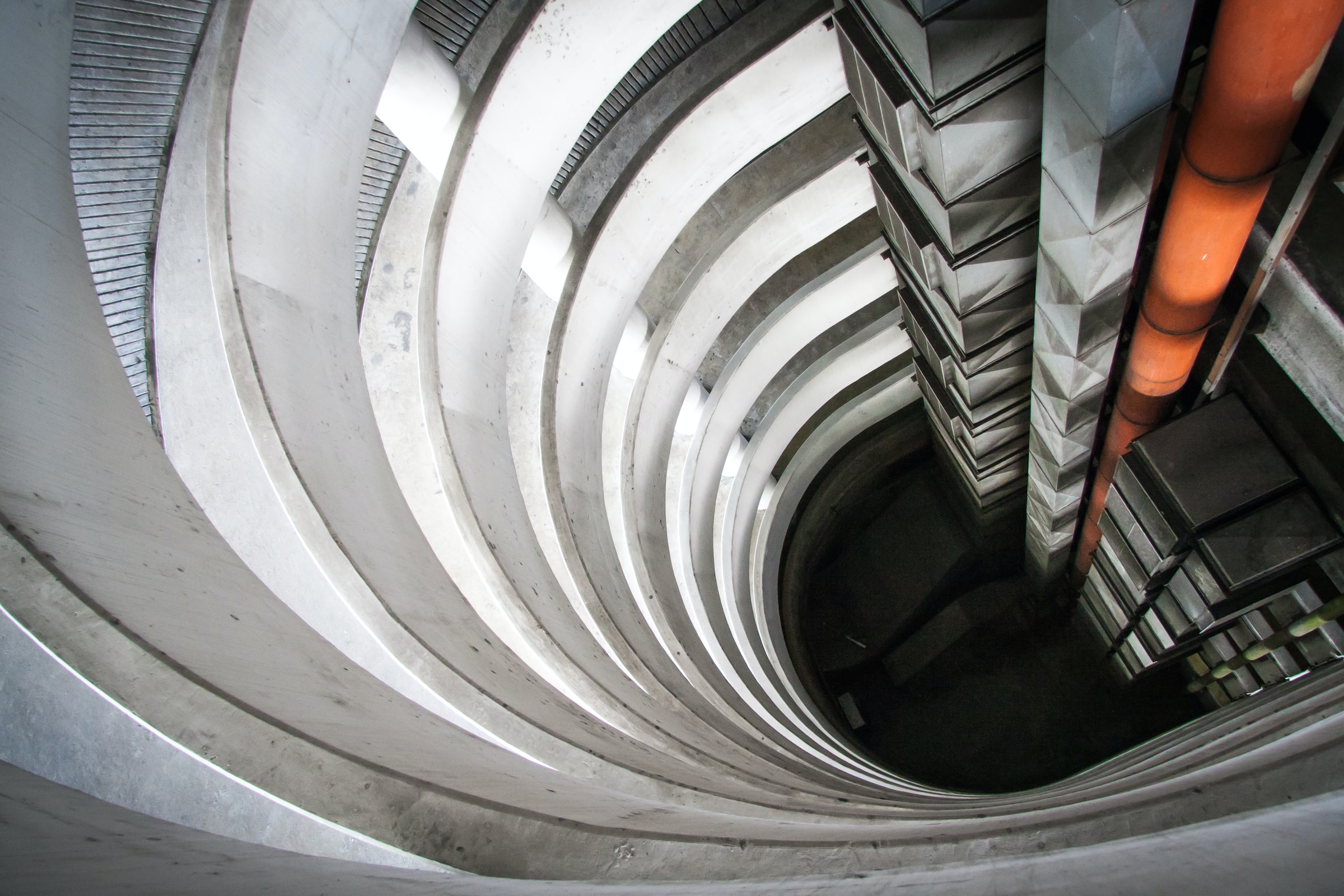
STEPS OF SAMPLE PREPARATION
PNEUMATIC TRANSPORT
The pneumatic tube installation enables the transport of carriers containing samples of various types to different tube stations within the pneumatic system. The technology is based on quick transportation using air as power source. A compressor generates the required pressure and suction for transport of the pneumatic carrier. Alternatively, the pneumatic system can make use of compressed air that is abundant in production plant. The product of differential pressure acting on the carrier and the cross-sectional area of the carrier has to be equal to the weight force of the carrier during upward movement and the friction forces. The pneumatic carriers have a waisted design that allows passing of turns and bends. The distance between the two protruding seal rings is usually 3 to 5 times the tube diameters. In general, this guarantees that carriers can transit bends with radii that are 5 to 10 times of the tube diameter.
Depending on whether a blower or compressed air is used, the speed of the pneumatic carrier can between 6 m/s and 20 m/s. In case of specially configured pneumatic systems and air tubes, an even higher velocity is possible. Usually, the external diameter of pneumatic tubes is 80 mm whereas the internal diameter is 75 mm.
PNEUMATIC TRANSPORT WITH COMPRESSED AIR AND DIVERTER
1. Sending station HR-HSK/B (on site)
2. Receiving station HR-HSK/L (laboratory site)
3. 2-way diverter
4. Tube connection set for compressed air/ laboratory site
5. Tube connection set/ on site
6. Profinet cable / optional: optical link
7. PrepMaster Terminal (optional)
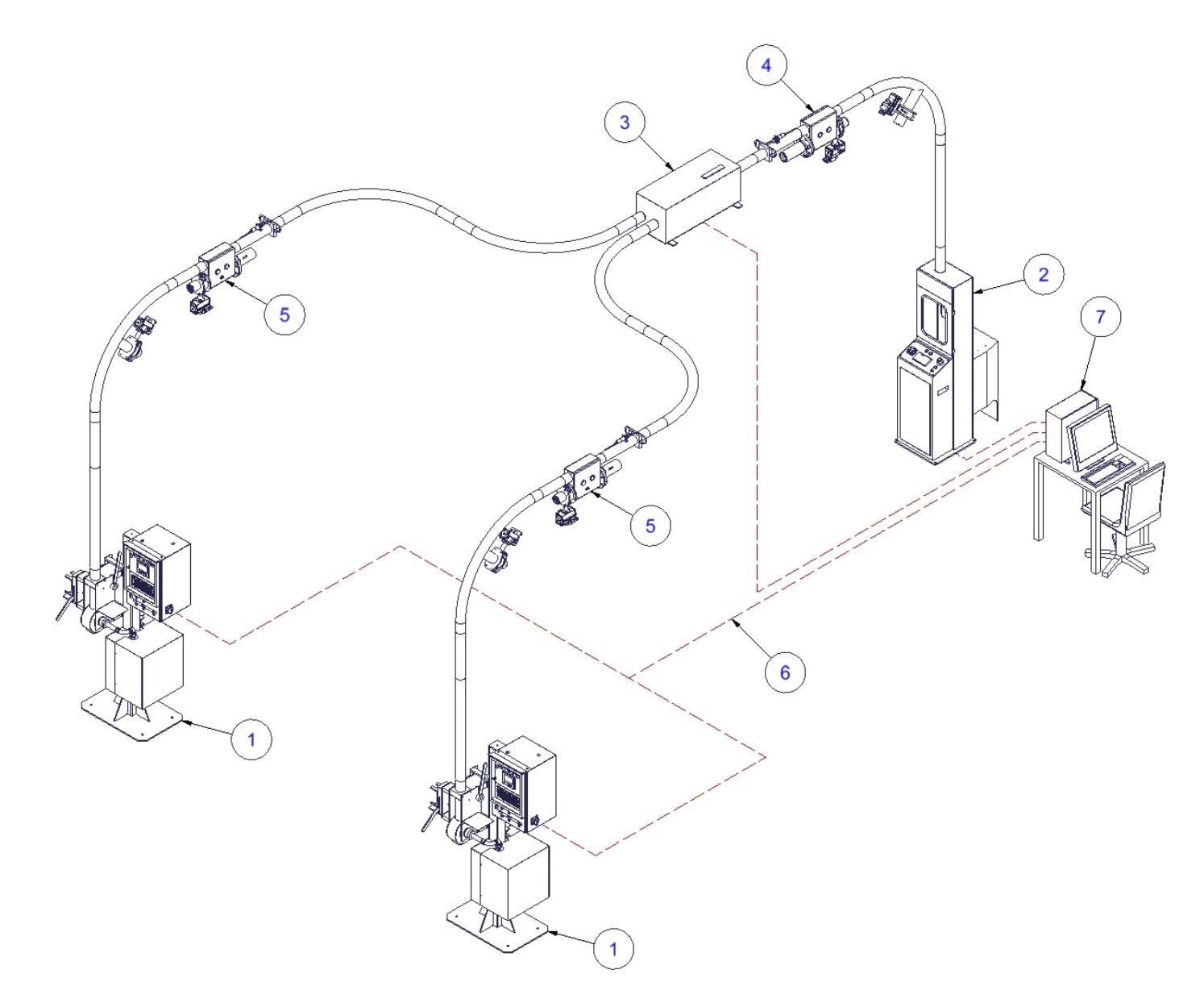
PNEUMATIC TRANSPORT WITH BLOWER AND DIVERTER
1. Sending station HR-HSK/B (on site)
2. Receiving station HR-HSK/L (laboratory site)
3. 2-way diverter
4. Tube connection set for compressed air/ laboratory site
5. Tube connection set/ on site
6. Profinet cable / optional: optical link
7. PrepMaster Terminal (optional)
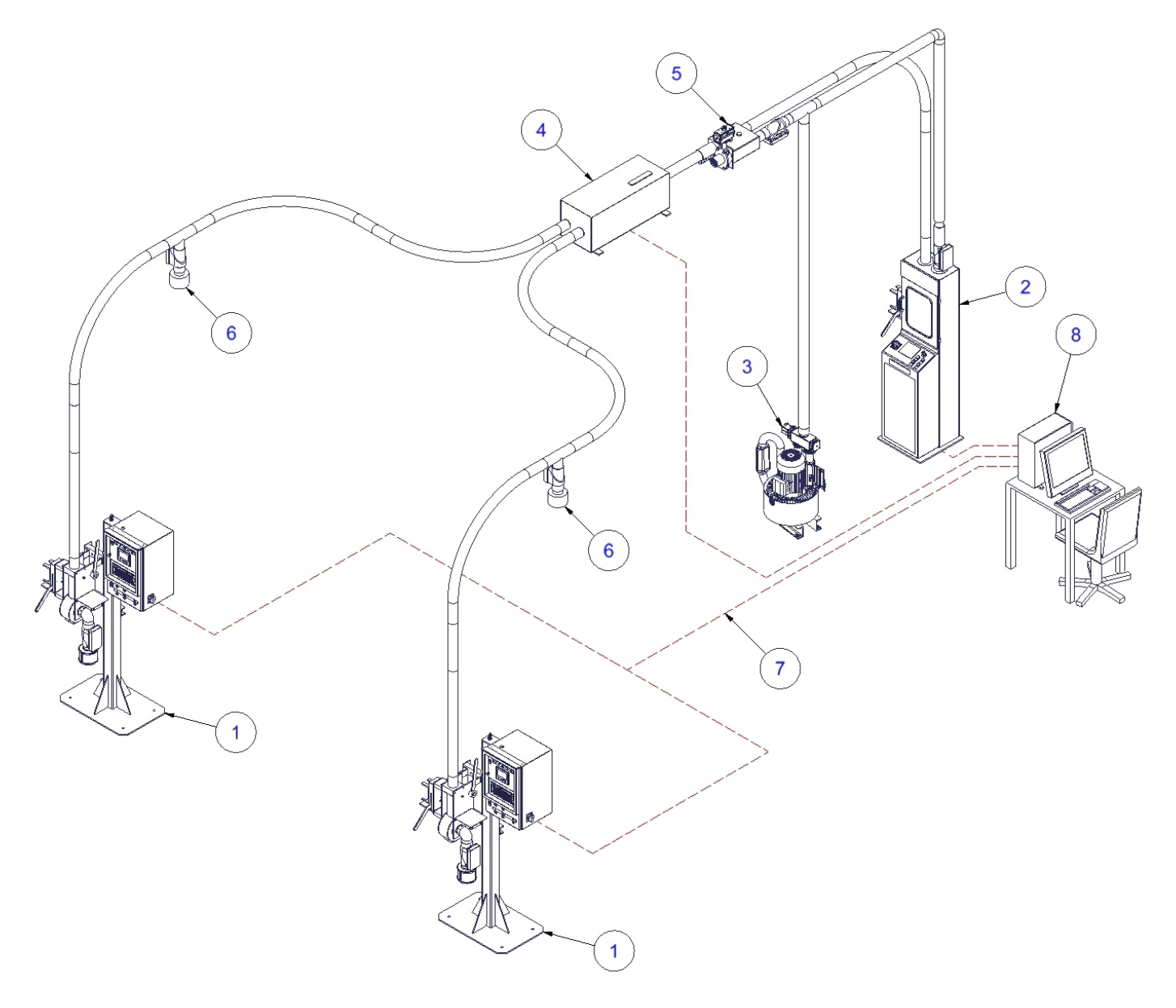
According to the sample type, different pneumatic carriers are available. For cold powder material and other light samples, we use carriers made from plastic. For hot powder and steel or iron samples, carriers are made from aluminum. For cement applications, usually 200 cc of sample material is sent to the laboratory. Pneumatic systems are available as manual or automatic versions. Using a manual system, the operator inserts the carrier manually into the plant station and removes it manually from the receiving station. Usually, the subsequent sample processing is manual as well. In case of automatic operation, different options are available. For powder material, the plant station covers automatic dosing, filling into carrier and transportation into the laboratory. Within the laboratory station, unpacking of the carrier and filling of the sample into a cup takes place. Then a transport system or robot forwards the cup for further sample preparation. After emptying and cleaning, the carrier is locked and sent back to the plant station. The control of the pneumatic system is due to the coordinated interaction between the PLC of the pneumatic station, the Scada system (PrepMaster) and the level 2 system of the client. The intelligent control of the system enables the efficient and quick sample transport into the laboratory.
PULVERIZING
The grinding process is a time- and cost-saving sample preparation procedure that is used in the analysis of cement and many other inorganic and organic materials. Prior to pressing, the material must be finely ground in order to guarantee sufficient homogeneity. HERZOG offers a wide variety of vibration mills in different sizes and configurations for the grinding of sample material. Along with the program parameters, the attainable fineness is also dependent on the following factors:
Material
- Input quantity
- Grinding aids used
- Grain size when put in
To perform the analysis by means of XRF, it is often necessary for the sample material to be ground to a grain size of < 75 μm. The grinding vessels must be made from wear-resistant materials in order to guarantee sufficient abrasion resistance. This applies particularly when the sample contains very hard mineral phases and has abrasive properties (e.g. clinker, silicon carbide, etc.). This means that during grinding, there is inevitably abrasion of the used grinding stones and of the grinding vessel. Depending on the application, the grinding vessel should be suitably hard and should have a chemical composition that does not contain any elements that are of analytical interest. Different grinding vessels are available in order to prevent the entry of elements that are relevant to the analysis.
With automatic mills, there is a choice between the following options:
- Spoon dosing (defines input quantity and allows blind sample)
- Pill dosing (precise dosing of grinding tablets)
- Sand cleaning (using quartz sand or other abrasive materials)
- Wet cleaning (using water and additives).
Automatic mills with input magazines also provide the possibility of batch processing. With this, several sample cups belonging to a sample batch can be ground without cleaning between each sample run. Besides minimizing the preparation time, this also helps to reduce possible material losses. Grinding aids have many different functions in the crushing of sample material. Grinding aids are used particularly with samples that have components with different milling properties. The amount of grinding aid used depends on the application and is usually between 2 % and 10 % of the sample quantity. Too much grinding aid results in weakening of the intensities and increases the detection limits of the analysis. Since just-pressed samples are used for the analysis of trace elements, dilution effects play a decisive role in the sample preparation. During pressing, the grinding aid tablets can be used in order to obtain a stable pellet. The use of grinding aid tablets containing wax offers the additional advantage that moisture absorption is reduced.
PELLETIZING
Depending on the analytical requirements, it is possible to choose between four standard pressing methods:
FREE PRESSING

Free pressing is the lowest-cost pressing method because no consumables are required. Precise dosing of the sample material is also not required.
TWO COMPONENTS PRESSING

2-component pressing: Pressing of 2 components requires an additional work step, but also offers the possibility of preparing small sample quantities for analysis. The refill magazine (e.g. boric acid, Boreox) is dosed and pre-pressed in an initial work step. A special pressing tool cover is used for this. The actual sample material is then pressed into the prepared matrix in a second pressing step.
PRESSING IN AN ALUMINIUM TRAY

Pressing in aluminium cups: For pressing in aluminium cups, the plunger should have a suitable venting groove in order to prevent compression of gases in the plunger. Aluminium cups are available in various diameters. Aluminium cups have the advantage that no significant costs are incurred if the samples are to be archived. Nevertheless, aluminium cups offer no guarantee with regard to eruptions occurring on the edges.
PRESSING IN STEEL RINGS

Pressing in steel rings: Using steel rings offers far-reaching advantages over the other pressing methods with regard to use in automated sample preparation systems. Using steel rings reduces the risk of contamination in the spectrometer by preventing eruptions on the sample edge. However, high costs are incurred if the re-useable rings must be archived. Two rings types are available for pressing in steel rings (Ø 40 mm & Ø 51 mm).
Cleaning steel rings: A three-stage brush system can be used to clean used steel rings after the analysis. This can be used with both manual and automatic presses. On manual presses, it is placed manually into the ring and is then removed manually. In automated pressing, the cleaning runs entirely without the operator’s intervention. The empty rings are then automatically stored in the internal magazine.
FUSION PROCESS
Fusion is an extremely efficient method of sample preparation for various analysis methods such as X-ray fluorescence, ICP and AA. The term fusion normally covers the mixing of a sample with a fusion agent, fusing the mixture and pouring in the form of a glass bead or dissolving in an acid solution.
Fusion is the best method when standards or sample material do not have a consistent matrix. This is normally the case with exploration, environmental and geological samples including mining material, minerals, clay, ores, dusts and waste materials. It is also often used with mixing materials such as cement, catalysts and electronic materials.
IMPROVING THE ANALYSIS RESULTS
Preparation with the aid of the fusion process results in a significant improvement in analytical accuracy. There are various reasons for this. Firstly, samples that have an identical chemical composition can differ from each other in terms of mineralogy and particle size. This alone can result in different counting rates in the analysis instrument. The fusion process eliminates these factors and thereby increases measuring accuracy. Secondly, dilution occurs in fusion through the addition of a fusion agent. This leads to a reduction in the interaction between the elements being analysed and a reduction in the so-called matrix effect. Thirdly, fusion makes it significantly easier to perform a calibration. On the one hand it is possible to produce perfect matrix-matched standards for a large number of materials. On the other hand, synthetic standards can be used if no referenced standards are available. Accordingly, synthetic standards can be produced for almost any material without the complex regression analyses for creating calibration curves.
AVOIDING ERRORS
Fusion is an extremely important part of material analysis by way of X-ray fluorescence, ICP and AA. Fusion is an excellent method for avoiding errors that can have a negative influence on the accuracy of the corresponding measuring method. Fusion is also the simplest and most reliable method for preventing errors arising from inhomogeneous particle distribution, mineralogical effects and insufficient surface quality.
IMPROVING THE SAMPLE SOLUTION
Fusion can easily dissolve oxidic samples that are difficult to prepare with the aid of acidulation. Conventional acidulation of resistant material such as silicates aluminium, zirconium etc. takes a long time and often only results in incomplete dissolving. However, complete sample dissolving is an extremely important factor for improving the accuracy and reliability of analysis results.
PERFECTLY SUITED TO FLUORESCENCE ANALYSIS
The fusion process produces a glass bead that is perfect for X-ray fluorescence instruments. The glass bead has the optimum dimensions, displays excellent homogeneity and has a flat surface.
TIME SAVING
A typical fusion process seldom takes longer than ten minutes. In contrast, acidulation takes hours before a satisfactory result can be obtained.
SAFETY
Fusion is a reliable sample preparation process that requires no harmful acids and reagents. Special safety measures are therefore not necessary. The fusion process is especially safe when it is done with apparatus that has automatic sample handling, fusing and pouring of the melt.
THE FUSION PROCESS
The most common method is borate fusion. This involves fusing a sample with an excess of lithium borate and in the form of a glass bead with a flat surface. During the fusion process, the sample’s material phases are converted into glass-like borate, which results in a homogeneous fusion bead that is perfectly suited to X-ray fluorescence analysis.
The finely ground sample material is first mixed in a crucible with a borate fusion agent (usually lithium), consisting of 95% platinum and 5% gold. The crucible is then heated to temperatures in excess of 1000°C until the sample is dissolved in the fusion agent. Movement of the melt during the fusion process improves the homogenisation of the material still further. A wetting agent (bromide, iodide, fluorine) can be added in order to support the separation of the melted material from the wall of the platinum material.